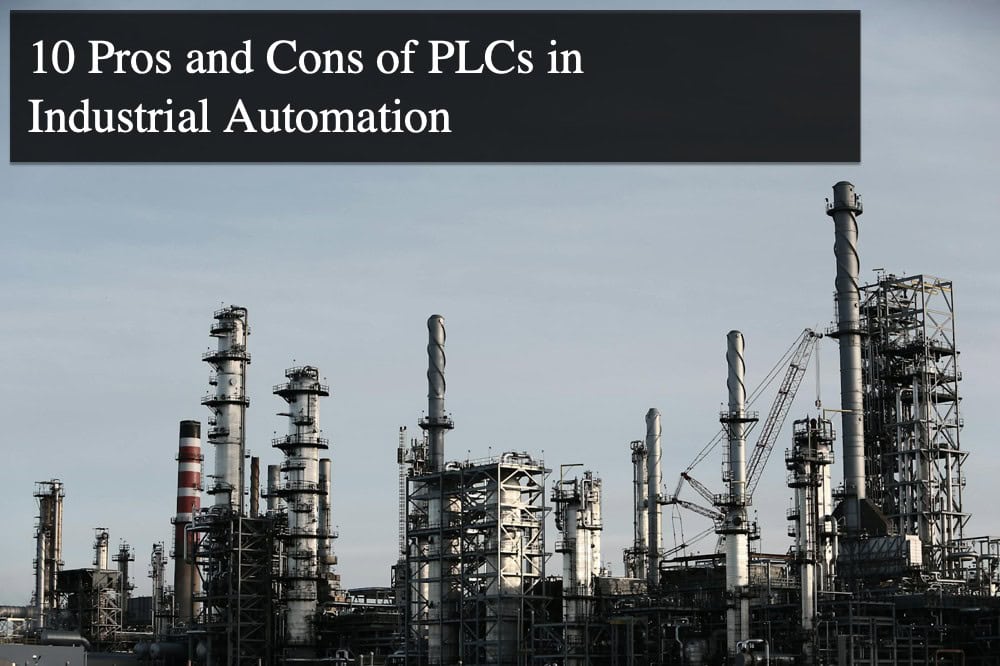
Programmable Logic Controllers (PLCs) play a key role in industrial automation. These rugged devices help control machinery, monitor processes, and improve efficiency. Designed for harsh environments, PLCs can withstand extreme temperatures, vibrations, and electrical noise, making them reliable for factory settings. Their ability to execute complex logic operations quickly allows industries to automate repetitive tasks with precision and consistency.
PLCs also enable seamless integration with other automation technologies, such as sensors, human-machine interfaces (HMIs), and supervisory control systems, enhancing overall productivity. They are widely used in manufacturing, energy, and other industries. But like any technology, PLC equipment has strengths and weaknesses. Letโs look at the top pros and cons of using PLCs in industrial automation.
10 Pros of PLCs in Industrial Automation
Reliability and Durability
PLCs are built to handle harsh industrial environments. They can withstand extreme temperatures, vibrations, and electrical noise. Unlike traditional relay-based systems, PLCs last longer and require less maintenance. Their rugged construction ensures they operate consistently even in demanding conditions such as chemical plants, automotive manufacturing, and food processing. This reliability reduces downtime and ensures production lines remain operational, which is crucial for meeting manufacturing targets and customer demands.
Flexibility in Programming
With PLCs, users can modify programs without changing physical wiring. Engineers can quickly update the logic to meet new requirements, reducing downtime. PLCs support various programming languages, such as ladder logic, structured text, and function block diagrams, allowing engineers to select the best approach for a specific application. Additionally, PLCs can be reprogrammed to accommodate new machinery or changes in production sequences.
High-Speed Operation
PLCs process data and execute commands rapidly. This speed is essential for applications that require real-time control, such as robotic assembly lines and conveyor systems. In industries like automotive manufacturing, PLCs enable precision timing for robotic arms. Their ability to process input and output signals within milliseconds makes them indispensable in high-speed automation environments where delays can lead to defective products or production bottlenecks.
Scalability
Companies can start with a basic PLC and expand its capabilities as needed. Adding more input/output (I/O) modules or integrating with other systems allows businesses to adapt to growth. For instance, a small manufacturing plant may begin with a basic PLC system, but as production expands, additional modules can be incorporated to handle more complex operations.
Remote Monitoring and Control
Modern PLCs offer connectivity options, including Ethernet and wireless communication. Engineers can monitor and troubleshoot systems from remote locations, which improves response times and reduces the need for on-site visits. In industries where facilities are spread across large geographic areas, such as oil refineries or water treatment plants, remote access enables engineers to make real-time adjustments and diagnose issues without having to be physically present.
Energy Efficiency
PLCs help optimize energy consumption by controlling machinery efficiently. Automated processes reduce waste and enhance sustainability in industrial operations. For example, PLCs can regulate motor speeds based on demand, preventing unnecessary energy consumption. In HVAC systems, PLCs can adjust heating and cooling levels based on occupancy and environmental conditions, leading to significant energy savings.
Easy Integration with Other Systems
PLCs can communicate with sensors, motors, and human-machine interfaces (HMIs). They also integrate with Supervisory Control and Data Acquisition (SCADA) systems. This interoperability allows industries to develop seamless production processes where different components work together efficiently. For example, in an automated packaging line, PLCs coordinate conveyor belts, robotic arms, and quality control sensors to ensure smooth operations without manual intervention.
Reduced Human Error
Automation with PLCs minimizes the risk of mistakes caused by manual control. This leads to greater consistency and quality in production processes. In traditional manufacturing, human errors can result in defects, rework, or safety hazards. By automating repetitive tasks, PLCs ensure that operations are executed accurately every time. This consistency is crucial in industries such as pharmaceuticals and food production, where precise measurements and procedures are required to maintain product quality and compliance with regulations.
Cost Savings Over Time
Although the initial cost of a PLC system can be high, it often reduces long-term expenses. Lower maintenance, fewer breakdowns, and improved efficiency result in significant savings. Traditional relay-based control systems require frequent replacements and manual rewiring, leading to higher maintenance costs. In contrast, PLCs are more durable and require fewer repairs. Additionally, the efficiency gains achieved through automation lead to increased production output.
Security Features
Many modern PLCs include security features such as password protection and encryption. These safeguards help prevent unauthorized access and cyber threats. In industries handling sensitive data or critical infrastructure, PLC security is essential to protect against potential cyberattacks. Implementing robust security measures, such as firewalls and authentication protocols, ensures that PLCs remain secure from external threats and unauthorized modifications.
10 Cons of PLCs in Industrial Automation
High Initial Cost
Purchasing PLCs and setting up automation systems can be expensive. The cost includes hardware, software, and training for employees. While PLCs offer long-term savings, the upfront investment may be a barrier for small businesses or those transitioning from manual processes to automation. Companies must carefully assess their budget and potential return on investment before implementing PLC-based automation.
Complex Programming for Beginners
PLCs use specific programming languages like ladder logic and structured text. Learning these languages requires training, which can be challenging for beginners. While experienced engineers can quickly program and troubleshoot PLCs, new users may struggle with the initial learning curve. Companies investing in PLCs must also invest in employee training to ensure their workforce can effectively operate and maintain the system.
Limited Processing Power for Advanced Applications
While PLCs handle basic and intermediate tasks well, some complex processes require more computational power. In such cases, industrial PCs or specialized controllers may be better options. Advanced data processing, machine learning, and artificial intelligence applications often require high-performance computing, which standard PLCs may not support. Companies must evaluate whether a PLC meets their processing needs or if alternative solutions are necessary.
Dependence on Software and Updates
PLCs rely on proprietary software for programming and updates. Compatibility issues can arise when upgrading systems or integrating new devices. If a manufacturer discontinues support for an older PLC model, companies may need to replace entire systems rather than simply upgrading software. Keeping PLC firmware and software up to date is essential to maintain security and functionality.
Potential Cybersecurity Risks
Connected PLCs are vulnerable to cyberattacks if not properly secured. Hackers can disrupt operations or steal sensitive data if security measures are weak. As more industrial systems connect to the internet, cyber threats become a growing concern. Companies must implement strong cybersecurity practices, including network segmentation, firewalls, and regular security updates, to protect their automation infrastructure.
Limited Customization Compared to Industrial PCs
PLCs follow a structured design, which may limit customization. Industrial PCs offer more flexibility for applications that require extensive computing power and complex software. If an operation requires highly specialized automation, an industrial PC with custom software may be a better option than a PLC.
Troubleshooting Challenges
While PLCs simplify many tasks, diagnosing issues in large automated systems can be difficult. Engineers need specialized knowledge to identify and fix problems efficiently. Companies must have skilled personnel available or rely on external experts for maintenance and troubleshooting.
Hardware Failures and Downtime
If a key PLC component fails, the entire system may shut down. Replacing parts can be costly and time-consuming, leading to potential production losses.
Limited Lifespan
PLCs, like any hardware, eventually wear out. Regular maintenance helps, but full replacements are necessary after years of operation.
Environmental Sensitivity
Extreme conditions, such as high humidity or electrical surges, can impact PLC performance and reliability, requiring protective enclosures or additional safeguards.
Conclusion
PLCs offer many advantages, including reliability, flexibility, and efficiency. They help businesses automate processes and reduce human errors. However, they also come with challenges, such as high initial costs and cybersecurity risks. With the right approach, businesses can maximize the benefits of industrial automation while minimizing potential drawbacks.
Suggested articles: Optimizing Project Management with Warehouseย Automation | 10 Best Practices for Success In Cloud Automation Testing
Daniel Raymond, a project manager with over 20 years of experience, is the former CEO of a successful software company called Websystems. With a strong background in managing complex projects, he applied his expertise to develop AceProject.com and Bridge24.com, innovative project management tools designed to streamline processes and improve productivity. Throughout his career, Daniel has consistently demonstrated a commitment to excellence and a passion for empowering teams to achieve their goals.