Top 5 Ways to Enhance Manufacturing Efficiency With Smart Technologies
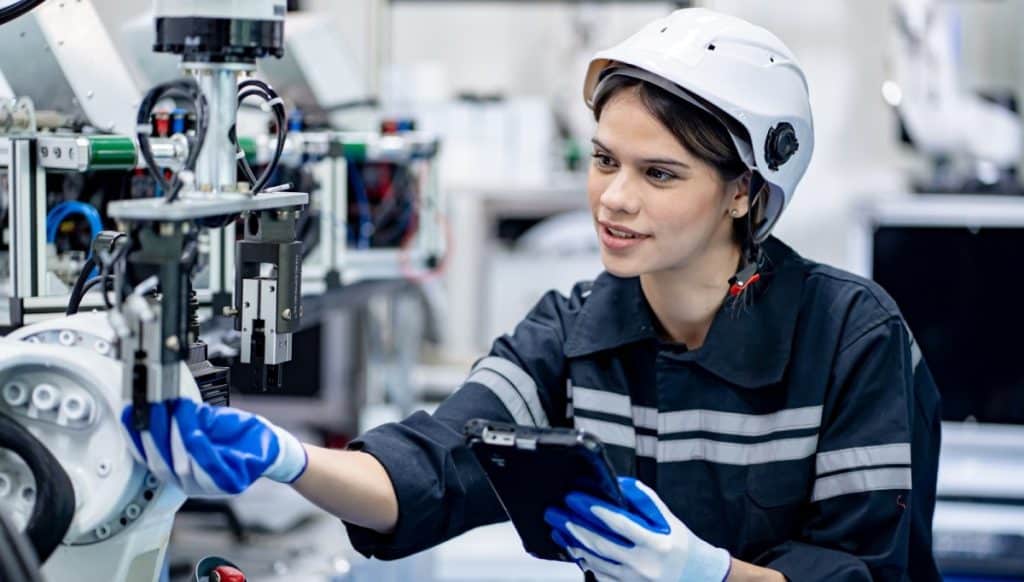
If you’re in manufacturing, you already know the pressure to produce faster, reduce waste, and keep quality high. But doing all that with outdated systems? That’s a losing game. Smart technologies aren’t just buzzwords. They’re real tools that help you cut downtime, automate routine tasks, and get better data to make smarter decisions.
In this blog, we’ll look at five proven ways smart tech is changing the game for manufacturers. Whether you’re just getting started or looking to level up, these ideas can improve how your shop runs, day in and day out. Let’s break it down into simple, practical steps.
Implementing Predictive Maintenance Software for Proactive Equipment Management
The old approach of repairing machines only after they break is quickly fading. Modern manufacturers are turning to smarter strategies, using advanced systems to predict and prevent issues before they happen. This proactive approach defines what is scheduled maintenance.
Predictive maintenance software represents a revolutionary approach to equipment management. By analyzing real-time data and historical patterns, these platforms can forecast when components are likely to fail, allowing maintenance teams to address issues proactively rather than reactively.
How AI-Powered Predictive Maintenance Reduces Unexpected Failures
Smart factories are installing networks of IoT sensors throughout their production lines, continuously monitoring equipment health. These sensors track everything from vibration patterns to temperature fluctuations, feeding data into advanced machine learning algorithms.
These algorithms become increasingly accurate over time, learning the unique “signature” of normal operations versus impending failures. A McKinsey study found that companies using AI-powered maintenance strategies experience a 10-40% reduction in maintenance costs and a 30-50% reduction in downtime (McKinsey & Company, 2023).
“The system warned us about bearing issues in a critical motor three weeks before it would have failed during peak production,” explains one manufacturing supervisor. “That single catch saved us nearly $80,000 in lost production time.”
Integrating Predictive Maintenance with CMMS Maintenance Software
The real power comes when predictive capabilities are incorporated into comprehensive CMMS maintenance software platforms. These integrated solutions provide maintenance teams with intuitive dashboards showing equipment health across the entire facility.
Modern CMMS systems don’t just flag potential problems; they automatically generate work orders, assign technicians, and order parts based on condition monitoring data. This seamless integration eliminates delays and miscommunications that often plague maintenance operations.
Many platforms now offer mobile interfaces, allowing technicians to receive alerts, access repair histories, and document services from anywhere in the facility. The result? Faster response times and more thorough documentation.
Utilizing Advanced Robotics and Automation for Precision Manufacturing
With maintenance challenges addressed, let’s explore how robotics and automation are transforming production capabilities in unprecedented ways.
Collaborative robots (cobots) are reshaping factory workflows by working alongside human workers rather than replacing them. Unlike traditional industrial robots that require safety cages, cobots are designed with advanced sensors that detect human presence and adjust their movements accordingly.
Collaborative Robots (Cobots) for Human-Machine Synergy
These robots excel at repetitive, physically demanding tasks, while human workers focus on complex decision-making and quality oversight. This synergy leverages the strengths of both humans and machines.
What makes cobots particularly valuable for small and mid-sized manufacturers is their flexibility. They can be quickly reprogrammed for different tasks, making them ideal for variable production environments where product changeovers are frequent.
The ergonomic benefits shouldn’t be overlooked, either. By taking over tasks that cause repetitive strain injuries, cobots are helping reduce workplace injuries and associated costs. One manufacturer reported a 35% reduction in workplace injury claims after deploying cobots for palletizing operations.
End-to-End Production Line Automation
Beyond individual robots, fully automated production lines represent the next frontier in manufacturing efficiency. Smart conveyor systems with real-time tracking capabilities allow managers to monitor work-in-progress inventory at every stage of production.
Vision systems using high-definition cameras and AI analysis can inspect products with greater precision than human eyes, catching microscopic defects at production speeds. These systems don’t get tired, distracted, or inconsistent.
The beauty of modern automation is its adaptability. Reprogrammable systems can quickly switch between different product variations, making small-batch production economically viable. This adaptability is crucial in today’s market, where product lifecycles are shorter and customization expectations are higher.
Implementing Best Work Order Software Systems for Streamlined Operations
As manufacturing equipment becomes more sophisticated, the systems managing maintenance and operations must evolve accordingly. The right best work order software creates the digital backbone that connects people, processes, and machines.
Modern facilities are moving beyond basic computerized maintenance systems to comprehensive platforms that optimize every aspect of operations. These advanced solutions deliver tangible benefits across departments.
Mobile-First Work Order Management Solutions
Today’s maintenance technicians aren’t chained to desktops. They need information while working directly with equipment. Mobile-first work order systems deliver everything they need through smartphones or tablets: repair histories, documentation, parts information, and even video tutorials.
The best platforms incorporate location-based prioritization, ensuring technicians tackle nearby problems first to minimize travel time. They also facilitate knowledge capture, allowing workers to document solutions and discoveries for future reference.
“We’ve cut response time by 40% since implementing mobile work order management,” reports one maintenance director. “Tasks that used to take days now happen within hours.”
Preventive Maintenance Scheduling That Maximizes Productivity
Preventive maintenance scheduling has evolved beyond simple calendar-based approaches. Today’s intelligent systems analyze production schedules, equipment usage patterns, and business priorities to identify optimal maintenance windows.
By integrating with production planning systems, these platforms ensure maintenance occurs during planned downtime rather than disrupting operations. AI-driven resource allocation algorithms optimize technician assignments based on skills, location, and workload.
The result? Maintenance events that once disrupted production now happen seamlessly in the background, with minimal impact on output and delivery schedules.
Analytics-Driven Performance Management
Modern work order systems don’t just track tasks—they generate insights. Customizable dashboards give managers real-time visibility into key performance indicators like mean time to repair, first-time fix rates, and maintenance costs per asset.
These analytics enable data-driven decisions about equipment replacement, process improvements, and resource allocation. Maintenance becomes a strategic function contributing directly to business goals, not just a cost center focused on keeping machines running.
Creating Smart Connected Factories Through IIoT Integration
Building on streamlined work order processes, manufacturers can achieve unprecedented operational visibility by connecting equipment, systems, and processes through Industrial Internet of Things (IIoT) networks.
These connected environments transform how factories operate, from monitoring individual machines to orchestrating entire production ecosystems. The resulting intelligence enables agility that was previously impossible.
Equipment Downtime Reduction Through Real-Time Monitoring
Equipment downtime reduction remains the most compelling IIoT use case for manufacturers. Connected sensors continuously monitor critical parameters like temperature, pressure, vibration, and power consumption.
Edge computing, processing data directly at the machine, enables instantaneous analysis and response without relying on cloud connections. When abnormal conditions emerge, automated workflows trigger appropriate actions, from simple notifications to emergency shutdowns.
Sophisticated root cause analysis tools help identify patterns across seemingly unrelated incidents, uncovering hidden issues that traditional approaches might miss. This deeper understanding allows manufacturers to address underlying problems rather than treating symptoms.
Energy Efficiency and Sustainability Monitoring
Smart factories aren’t just more productive, they’re more sustainable. IIoT systems monitor energy consumption at granular levels, identifying waste and optimization opportunities in real-time.
Peak demand management systems automatically schedule energy-intensive processes during off-peak hours when rates are lower. Some platforms can even integrate with renewable energy sources, prioritizing operations when clean energy is abundant.
For companies pursuing sustainability certifications, these systems provide the detailed documentation required to demonstrate improvements in carbon footprint and resource utilization.
Data-Driven Decision-Making with Manufacturing Analytics
As we’ve seen, smart manufacturing generates enormous volumes of data. The final piece of the puzzle is transforming this information into actionable intelligence through advanced analytics platforms.
Production Performance Dashboards and Visualization
Real-time dashboards tracking Overall Equipment Effectiveness (OEE) give managers immediate visibility into production performance. Custom views can be created for different roles, from operators focusing on single machines to executives monitoring facility-wide metrics.
These visualizations remove guesswork from decision-making, highlighting opportunities and challenges that might otherwise remain hidden in spreadsheets or databases.
Machine Learning for Process Optimization
Machine learning algorithms can analyze thousands of process variables simultaneously, identifying optimal operating parameters that human engineers might never discover through traditional methods. These insights lead to improved yields, reduced waste, and higher quality.
Anomaly detection systems constantly monitor for deviations from established norms, flagging potential issues before they impact production. This predictive capability allows for intervention before quality or efficiency suffers.
Predictive Quality Assurance Systems
Quality no longer needs to be inspected at the end of production. AI vision systems can monitor product characteristics throughout manufacturing, identifying potential defects in real-time.
Statistical process control integration allows for automatic adjustments to maintain quality within specified parameters. More advanced systems can even predict potential quality issues based on subtle changes in process variables, enabling preventive action before defects occur.
Moving Manufacturing Into the Future
Smart manufacturing technologies are no longer future trends, they’re delivering real results today. From predictive maintenance to work order software, these tools boost efficiency and cut downtime. Success starts with assessing current systems, identifying gaps, and creating a clear roadmap with measurable goals.
A phased approach, starting with high-impact areas, ensures alignment with business needs. Manufacturers that act now will stay agile, meet customer demands, and maintain a competitive edge in a fast-changing market. The time to modernize isn’t later, it’s now.
FAQs on Smart Manufacturing
How is smart technology used in manufacturing?
Smart manufacturing solutions use artificial intelligence and machine learning to contextualize information and provide actionable insights, enabling you to predict machine failures to get ahead of maintenance, adjust production schedules, and avoid costly downtimes.
How has technology made manufacturing more efficient?
A prime example of automation in manufacturing is robots, which can perform tasks faster, more efficiently, and with less risk to humans. By reducing cycle time, labor productivity, and labor costs, robots can speed up production by reducing the time required to manufacture a product.
How can manufacturing be more efficient?
Manufacturing efficiency improves through several key strategies: reducing production waste, identifying bottlenecks, improving employee attendance, implementing automation, using specialized manufacturing software like CMMS maintenance software, staying organized, preventing equipment breakdowns, and offering thorough employee training.
Suggested articles: The 5 Roles of IT Support in Automating Manufacturing Processes | The Importance of Cloud Computing for Scalable AI Edge Solutions