Staying on Track: Managing Costs, Time, and Quality in Manufacturing Projects
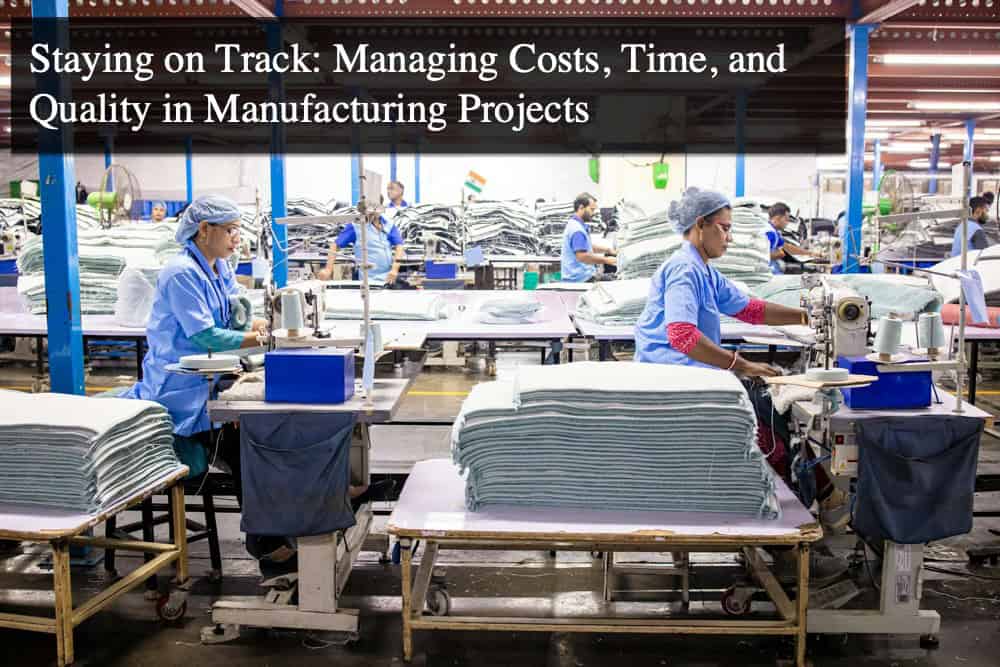
Every manufacturing project lives under the shadow of three non-negotiables: budget, schedule, and quality. Hit all three, and you’ve got a win. Miss one, and the whole project can feel off-kilter. For project managers, the challenge isn’t just delivering — it’s balancing. How do you move fast without overspending? Cut costs without compromising quality? That’s where strategy steps in.
Managing Cost Without Cutting Corners
Manufacturing budgets are notoriously tight. Labor, raw materials, energy, and logistics all add up. The key is visibility. Instead of reacting to overruns, managers need real-time insight into costs. Build a detailed budget early and revisit it often. If spending starts to veer off course, quick adjustments can prevent bigger issues later.
Lean principles help, too. Reducing material waste, streamlining workflows, and trimming non-essential processes can make a real difference. But smart savings don’t mean cutting corners. Underpaying for materials or labor might look good on paper until delays, breakdowns, or rework start stacking up.
This is where automation pays off. Smart tools like packaging machines from Paxiom.com can reduce manual labor, improve consistency, and increase throughput without driving up operating costs. It’s an investment, but one that protects both your budget and your bottom line.
Example: A craft brewery needed to scale up production of canned beverages but faced high labor costs for manual packaging. The project manager implemented a Paxiom automated packaging machine, reducing labor expenses by 30% while maintaining consistent can seals. This kept the budget in check without sacrificing the quality of the final product.
Keeping Projects on Schedule
Delays are a fact of life in manufacturing, but they don’t have to be the norm. The best way to stay on time is to start with a schedule that accounts for reality, not just optimism. Build in buffers. Get input from the floor. And don’t forget that one delay often creates a ripple effect, especially if it hits a task on the critical path.
Technology helps here, too. Project management platforms, production dashboards, and automated alerts can keep everyone aligned and accountable. They surface problems early so you can shift resources or reorder tasks before you fall behind.
Strong communication is just as vital. A late delivery from a supplier, a maintenance delay on a key machine — these things happen. But when the team is looped in and empowered to respond quickly, delays don’t spiral. They get handled.
Example: During a project to produce custom aluminum enclosures for a tech company, a supplier delayed delivery of raw materials by a week. The project manager, using a project management platform with real-time alerts, quickly reallocated resources to prep other components and communicated with the client to adjust expectations, keeping the project on schedule for final delivery.
Meeting Quality Standards Consistently
Quality isn’t just about the final product — it’s about how you get there. Define what success looks like from the start. Make sure your team knows the benchmarks and what’s expected at each phase.
Don’t wait for the end of the line to check if something’s gone wrong. Build in quality checkpoints along the way. A small defect caught early is easier and cheaper to fix than a full batch of unusable output.
Training matters, too. A well-trained team makes fewer mistakes, catches problems faster, and works more efficiently. Empower people on the line to speak up when something looks off. A culture of quality isn’t built on inspection — it’s built on ownership.
Example: A furniture manufacturer producing high-end custom chairs for a hotel chain implemented quality checkpoints during the wood staining and upholstery stages. When a worker noticed inconsistent stain application early in the process, the team corrected it immediately, preventing costly rework on 200 chairs and ensuring the client’s quality standards were met.
Balancing the Trade-offs
Here’s the truth: You can’t maximize cost savings, speed, and quality all at once. Trying to do so usually means sacrificing all three. Instead, choose what matters most for each project. If hitting a delivery deadline is non-negotiable, budget for overtime or automation. If quality is the top priority, extend the timeline slightly to reduce rework risk.
Project managers should keep these trade-offs visible and involve stakeholders in the conversation. When everyone understands the why behind a decision, they’re more likely to support it, even if it means shifting expectations.
Example: A medical equipment manufacturer prioritized quality for a batch of surgical tools, extending the timeline by one week to allow for additional testing. The project manager presented the trade-off to the client, explaining how it ensured compliance with strict regulatory standards. The client agreed, and the tools passed all inspections, avoiding costly recalls.
Making It Work in the Real World
Manufacturing projects rarely go perfectly, but with the right mindset, they can stay on track. Managing cost, time, and quality isn’t about controlling every detail. It’s about constant adjustment, clear priorities, and the smart use of tools and talent. When those elements line up, success follows — on time, on budget, and built to last.