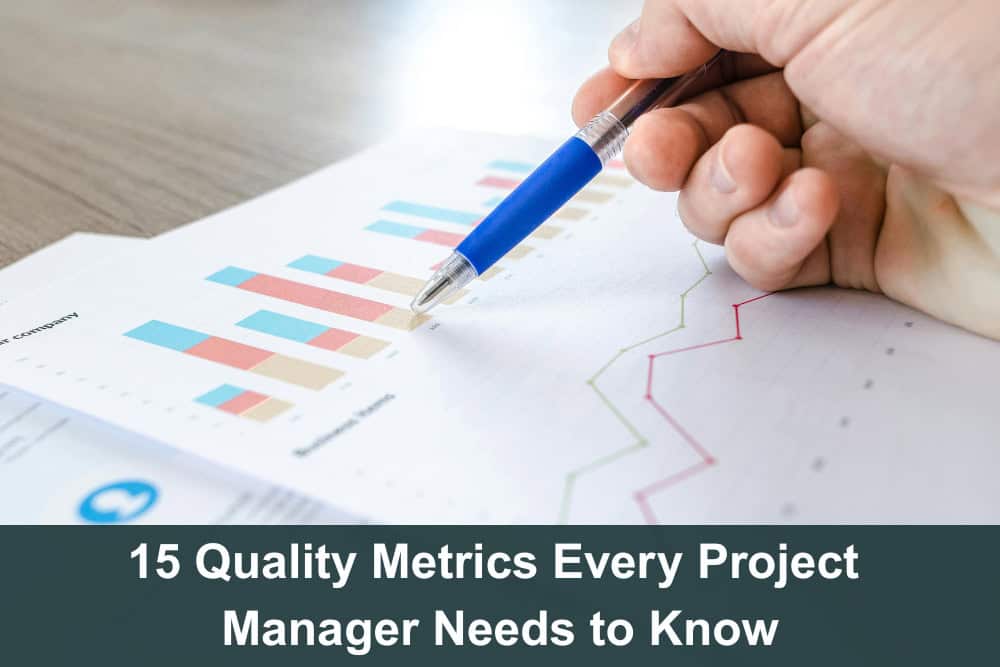
In project management, quality metrics measure a project’s success in meeting its goals. Various quality metrics can be used, and the choice of metric will depend on the project’s specific goals. Standard quality metrics include customer satisfaction, cycle time, failure rate, quality control, defect density, etc.ย Each metric measures something different, but all are important in ensuring the success of your project and the quality of deliverables.
By tracking and measuring the quality of your project, you can identify potential problems and risks and take the right steps to mitigate them.ย
What are Quality Metrics?
Quality metrics are a vital part of project management. By tracking and measuring the quality of your project, you can identify potential problems and risks and take the necessary actions to reduce them. This can massively help avoid costly delays or errors.
Explained: By tracking quality metrics, you can ensure that your project is always moving in the right direction and that any problems are quickly addressed. Quality metrics can also help you evaluate the effectiveness of your quality management process and make improvements where needed.
Importance of Using Quality Metrics
As a project manager, using quality metrics to ensure your project is on track and meeting all objectives is essential. By tracking metrics, you can identify issues early on and take corrective action to prevent them from becoming serious problems.
- Quality metrics can be used to assess various aspects of your project, such as the quality of your products or services, the performance of your team, the satisfaction of your customers, and more.
- They can also help you benchmark your project against similar projects and track your progress over time.
- Quality metrics provide a quantifiable way to track and improve the quality of your project.
If you’re not already using quality metrics in your project management, now is the time to start.
15 Quality Metrics to Consider in Your Next Project
There is no single quality metric that is perfect for all projects. The best metric will depend on the project, but PM-Training has collected 15 of them with an example to give you a clear picture of what and how to use them.
1. Schedule Performance
- What is it? The Schedule Performance Index (SPI) is a project management tool used to measure a project’s progress against its schedule. The SPI is calculated by dividing a project’s earned value (EV) of a project by the planned value (PV). The resulting number is then multiplied by 100 to get a percentage.
- Main uses: The SPI can assess a project’s health and identify potential problems. A low SPI indicates that a project is falling behind schedule, while a high SPI suggests that a project is ahead of schedule. The SPI can also be used to compare the progress of different projects.
- Example: SPI is calculated by dividing a project’s earned value (i.e., the value of the work that has been completed) by its planned value (i.e., the value of the work that was scheduled to be completed).
2. Productivity Measures
- What is it? Productivity measures how efficiently resources are used to produce a desired output. In project management, productivity is often used to measure a project’s progress or to compare the efficiency of different project management methods.
- Uses: Several different productivity metrics can be used, but the most common is output per unit of time. This metric compares the amount of work produced in a given period (usually an hour) to the amount of time worked, typically measured using time tracking systems.
- Example: If a worker produces two work units in an hour, their productivity would be two units/hour.
3. Customer Satisfaction Surveys
- What is it? Customer satisfaction surveys are a standard quality metric to gauge how well a project meets its users’ needs.
- When to use: It can be used in project management to gauge whether a project meets its customers’ needs. If its score is low, it may indicate that the project is not meeting customer expectations and needs to be improved. Conversely, a high Customer Satisfaction score shows that the project meets customer needs and can be successful.
- Example: It can be calculated by surveying customers and asking them to rate their level of satisfaction on a scale of 1 to 5 (1 being very unsatisfied, 5 being very satisfied).
4. Cycle Time
- What is it? Cycle time is the metric used in agile project management to measure the time it takes to complete a task. This metric is used to help agile teams optimize their workflow and improve their efficiency.
- When to use: Cycle time measures the amount of time it takes to complete a sprint or a specific task. It is often used to identify areas for improvement in the project management process. To calculate the cycle time for an individual task, take the days to complete it from start to finish.
- Example: If a company aims to increase customer satisfaction, it may implement a process that includes cycle times for each customer journey stage. This could consist of the time it takes to receive a customer complaint, investigate the issue, resolve it, and follow up with the customer.
5. Cost Control Measures
- What is it? The cost control metric is valuable for monitoring and controlling project costs and keeping projects on track.
- When to use: This can be done monthly or even weekly. By tracking the cost control metric, you can quickly see if the project is on track to stay within its budget.
- Example: One example of cost control in project management is creating a budget, monitoring project spending, and using earned value management techniques. By using these and other cost control measures, project managers can help ensure that their projects stay on track and budget.
6. On-Time Performance
- What is it? The On-Time performance metric measures how well a project delivers its planned, timely outputs. This metric is a valuable tool for project managers as it allows them to track the progress of their project and identify any potential risks of delays.
- When to use: To use the ON-TIME performance metric, project managers should first identify the total number of planned outputs for their project. They should then track the number of outputs delivered on time and divide this by the total number of planned outputs. The resulting number will give the project manager an indication of how well their project is performing on-time delivery.
- Example: One way is to create a baseline for future projects, like Software. Knowing how well previous projects have met their schedules allows you to set more realistic expectations for future projects.ย
7. Failure Rate
- What is it? The failure rate is a metric that measures the number of failures in a given process or system. It is typically expressed as a percentage or a ratio and can be used to track a process or system’s performance over time.
- When to use: The failure rate can be used in project management to help identify potential problems and mitigate risks. It can also help you to understand the root causes of failures and identify opportunities for improvement.
- However, it is essential to understand how to interpret the failure rate and how it can be used with other metrics to get the most accurate picture of a process or system.
- Example: One example of a failure rate in project quality management is if the percentage of defects in a product or service exceeds the acceptable limit. This can happen due to several factors, including poor design, inadequate testing, or production errors. It can lead to substantial losses for a company and decreased customer satisfaction.
8. Defect Frequency
- What is it? The defect frequency metric measures the number of defects per unit of time. It is often used in project management to track a project’s progress and identify areas for improvement.
- How to use: To calculate the defect frequency metric, you must first identify the total number of defects for a given period. This can be done by looking at the project’s bug tracker or by reviewing the project’s code. Once you have the total number of defects, you can calculate the defect frequency by dividing the total number by the total project duration.
- Example: Defect frequency can also be measured by the number of defects per unit of product. For example, if a product has 100 defects, and there are 1,000 units of that product, the defect frequency would be 100/1,000.
9. Quality Control
- What is it? This is very general in Quality, as many different quality control metrics can be used to measure a project’s quality. Some standard metrics include the number of defects, the number of customer complaints, and the cost of quality. Quality control metrics can be used to assess the quality of a project at any stage of development.
- When to use: They are typically set at the beginning of a project and are used to guide the team throughout the project and need to be used to track progress, identify quality problems early, and prevent quality issues from occurring.
- Example #1: Cycle time: It takes time to complete one process cycle. It can be used to measure a process’s efficiency and identify areas for improvement.
- Example #2: Yield: This is the percentage of products or services that meet quality standards. It can be used to measure the overall quality of a project.
- Example #3 Defect rate: This is the number of defects per output unit. It can be used to identify areas for quality improvement.
10. Defect Rate
- What is it: In quality management, the defect rate is the number of defects per unit of output. Defects can be anything from cosmetic flaws to major product failures. The defect rate is a measure of quality that can be used to assess the performance of a manufacturing process or a product.
- How to use: There are several ways to calculate defect rate, but the most common method is to use the following formula: defect rate = number of defects/number of opportunities. This formula gives you the average number of defects per unit of work. opportunities. It can be used for projects of any size.
- Example: Defect rate is usually measured as the number of defects per unit of work. For example, if you have a project with 100 defects and you divide it into 10 work units, then the defect rate would be 10 defects per unit.
11. Error Value
- What is it: In Project Quality Management, the Error Value is a measure of the accuracy of the work performed. There are three main factors that contribute to the Error Value:
- The skill of the worker
- The quality of the materials used
- The methods used to perform the work
- When to use: This value determines whether the work is within the project’s acceptable tolerance range. If the Error Value is too high, it means that the work is not accurate enough and needs to be improved. The Error Value is calculated by taking the sum of the squares of the three factors mentioned above. This value is then divided by the total number of projects in the quality management system.
- Example: So, considering the formula for an error value is: Error Value = (1 – (Accuracy of Deliverable / 100)) * 100, then, for example, if a project deliverable has an accuracy of 85%, the error value would be 15%.
12. Scrap Rate
- What is it: Scrap rate is a measure of the percentage of material that is wasted during a manufacturing process. It is typically expressed as a percentage of the total amount of material used.
- Use: While the scrap rate can be a useful metric for project managers, it is important to remember that it is not always accurate. Several factors can affect the scrap rate, including the type of product being manufactured, the manufacturing process, and the quality of the materials. In addition, the scrap rate can vary from one company to another, so it is important to compare apples to apples when using this metric.
- Example: For example, if a manufacturing process uses 100 pounds of raw material and 5 pounds of waste is generated, the scrap rate would be 5%.
13. Lead Time in Agile
- What is it? Lead time is the amount of time that passes between the start of a project and its completion. It can also be the amount of time that passes between the start of a project and the delivery of the final product. Lead time can be used to measure a project team’s efficiency and track a project’s progress.
- When to use: Lead time can be used in project management to help schedule future projects and estimate the time a project will take to complete. It is also often used to calculate a project’s due date.
- Example: Lead time can also refer to the time that passes between the start and finish of a project. For example, a project with a long lead time may be more expensive to complete, whereas a project with a short lead time may be less costly.
14. Test Coverage (QA)
- What is it? Test coverage is a metric that measures the amount of code covered by tests in a feature. It is a useful tool for project managers because it can help them assess a project’s risks and prioritize testing efforts.
- When to use: There are a few different ways to measure test coverage, but the most common is to use the percentage of code covered by tests. This metric can be used to compare the amount of coverage between different projects or to track the coverage of a project over time. The higher the test coverage, the more confidence you can have in your tests.
- Example: One example of how test coverage is essential in Project Management can be seen in the case of a software development project. In software development, test coverage is the degree to which the software tests exercise the code. A high degree of test coverage means that most of the code has been tested and is more likely to be defect-free. For example, a project manager can require tests to cover all new code before it is accepted into the codebase.
15. Code Coverage
- What is it? Code coverage is a metric used to measure the amount of code executed during a test. It is typically expressed as a percentage and is a good way to gauge a test’s completeness.
- Uses: Code coverage can be used in project management to help prioritize testing and ensure that all project aspects are being tested.
- Example: In general, this metric counts the number of lines of code that are executed during a test. Another way to measure code coverage is branch coverage, which counts the number of branches (if-then-else statements) executed during a test.
Why are They Essential for Your Project?
Quality metrics can measure various aspects of your project, including its scope, schedule, cost, and performance. By tracking these metrics, you can identify trends and patterns that can help you improve the quality of your project. They can also help you communicate the success of your project to stakeholders and clients.
What are the Disadvantages of Using Quality Metrics in Project Management?
Although quality metrics have many benefits, they also have some challenges. They can be time-consuming to set up and maintain, and difficult to interpret, especially if you don’t have a solid understanding of statistics. Despite these challenges, quality metrics are a valuable tool that can help you improve the quality of your project.
Suggested articles:
- What Are the Most Overlooked Metrics in Evaluating Project ROI?
- 7 Essential Quality Acceptance Criteria Examples
- 8 Mandatory Metrics for Successful Project Execution
Shane Drumm, holding certifications in PMPยฎ, PMI-ACPยฎ, CSM, and LPM, is the author behind numerous articles featured here. Hailing from County Cork, Ireland, his expertise lies in implementing Agile methodologies with geographically dispersed teams for software development projects. In his leisure, he dedicates time to web development and Ironman triathlon training. Find out more about Shane on shanedrumm.com and please reach out and connect with Shane on LinkedIn.